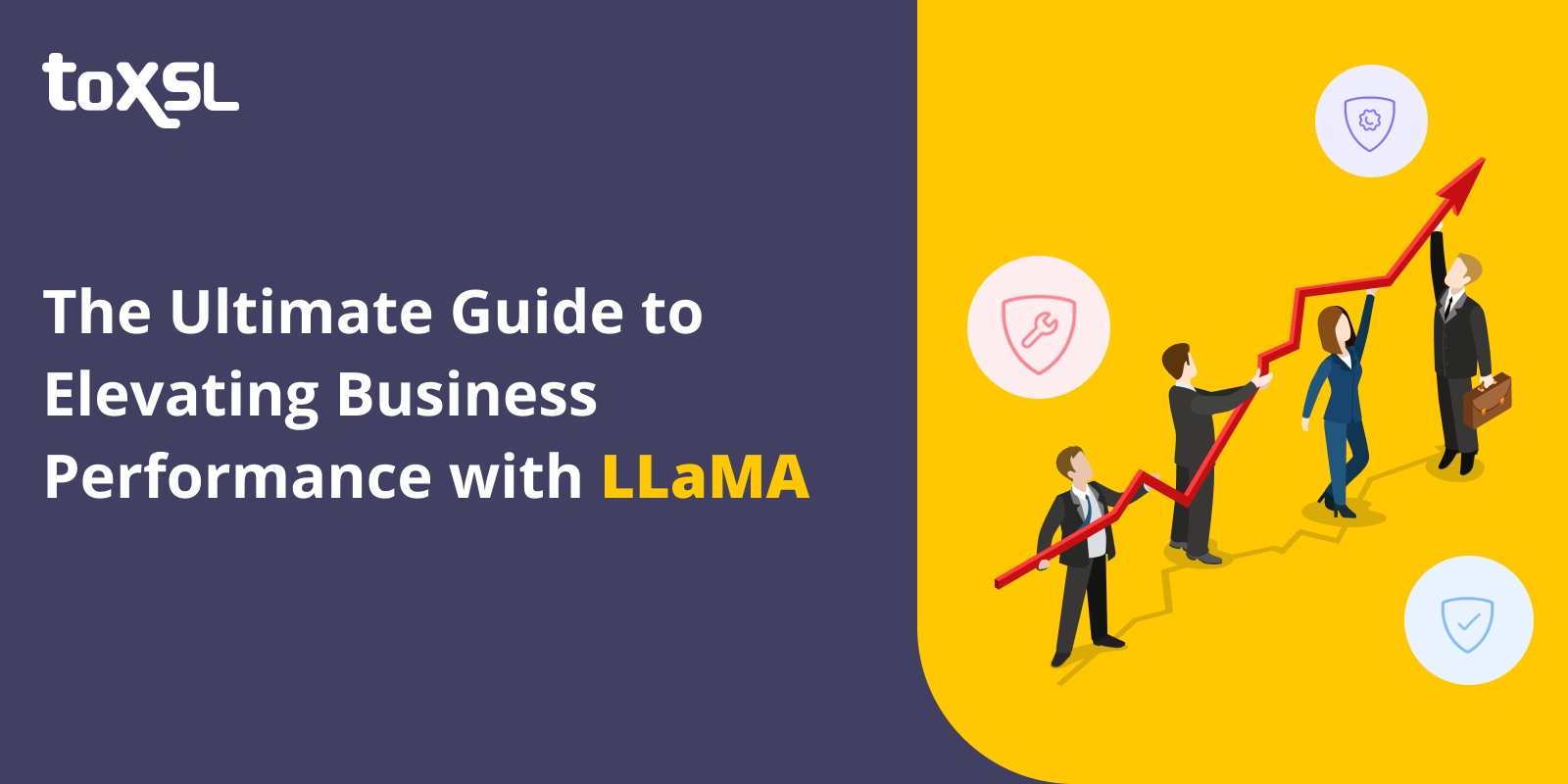
In today’s highly competitive business landscape, organizations are constantly seeking innovative ways to enhance their performance and gain a competitive edge. One such approach that has gained significant attention is the use of LLaMA (Lean, Agile, and Six Sigma) methodologies. LLaMA combines the principles of Lean, Agile, and Six Sigma to drive operational excellence, improve efficiency, and deliver superior customer value. This comprehensive blog will delve into the various aspects of LLaMA and how it can be leveraged to enhance business performance across different industries.
Understanding LLaMA Methodologies
LLaMA represents a powerful fusion of three distinct methodologies - Lean, Agile, and Six Sigma. Each of these methodologies brings its own set of principles and practices that are aimed at optimizing processes, reducing waste, and achieving continuous improvement.
Lean is centered around the concept of eliminating waste and non-value-added activities from
processes. It emphasizes the importance of creating flow in operations, minimizing inventory, and continuously improving processes to deliver maximum value to customers.
Agile methodologies originated in the software development realm but have since been adopted across various industries. Agile focuses on iterative and incremental development, collaboration, flexibility, and customer feedback. It enables organizations to respond quickly to changing market dynamics and customer needs.
Six Sigma is a data-driven methodology that aims to minimize defects and variations in processes. It relies on statistical tools and techniques to identify root causes of problems, standardize processes, and achieve consistent quality outputs.
The Synergy of LLaMA
When these three methodologies are integrated into LLaMA, they create a powerful framework that addresses different aspects of business operations. Lean principles help in streamlining processes and eliminating waste, Agile methodologies enable flexibility and responsiveness to changing market demands, while Six Sigma ensures high-quality outputs through data-driven decision-making.
The synergy of LLaMA allows organizations to benefit from the strengths of each methodology while mitigating their individual limitations. By leveraging this integrated approach, businesses can achieve operational excellence, improve customer satisfaction, reduce costs, and drive sustainable growth.
Enhancing Business Operational Efficiency with LLaMA
One of the key benefits of implementing LLaMA methodologies is the significant enhancement in operational efficiency. Lean principles enable organizations to identify and eliminate non-value-added activities, thereby streamlining processes and reducing lead times. Agile methodologies facilitate quick adaptation to changing customer requirements and market dynamics, enabling faster product development cycles and improved time-to-market. Six Sigma ensures that processes operate within defined tolerances, leading to reduced defects and higher process capability.
By integrating these methodologies under the LLaMA framework, businesses can optimize their operations for maximum efficiency. This not only leads to cost savings but also enhances overall productivity and resource utilization.
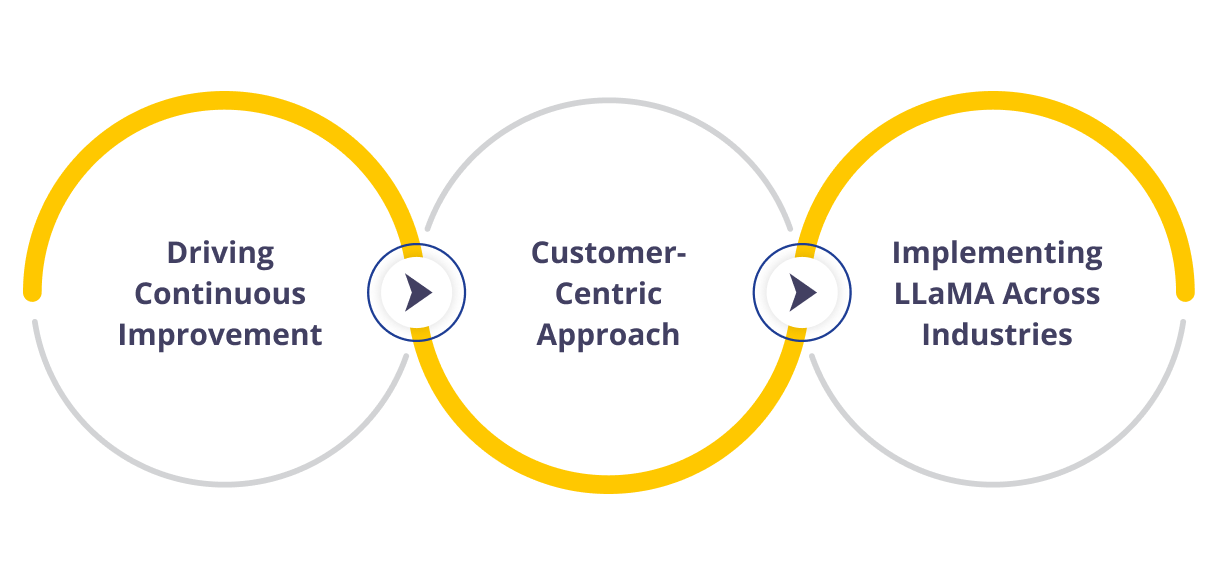
Driving Continuous Improvement
Continuous improvement is at the core of LLaMA methodologies. Lean promotes a culture of continuous improvement by empowering employees to identify inefficiencies and implement solutions. Agile’s iterative approach encourages ongoing refinement based on customer feedback and evolving requirements. Six Sigma’s focus on data-driven decision-making ensures that improvements are based on factual analysis rather than assumptions.
Through LLaMA, organizations can institutionalize a culture of continuous improvement where every employee is encouraged to contribute towards enhancing processes, products, and services. This relentless pursuit of excellence enables businesses to stay ahead of the competition and adapt proactively to market changes.
Customer-Centric Approach
LLaMA methodologies emphasize a customer-centric approach to business operations. Lean principles align with delivering value to customers by eliminating waste and focusing on what truly matters to them. Agile methodologies promote close collaboration with customers throughout the development process, ensuring that their evolving needs are met effectively. Six Sigma’s emphasis on quality directly translates into delivering products and services that consistently meet or exceed customer expectations.
By adopting LLaMA, organizations can embed a strong customer focus into their operations, leading to higher customer satisfaction levels, increased loyalty, and positive brand perception.
Implementing LLaMA Across Industries
The versatility of LLaMA makes it applicable across diverse industries ranging from manufacturing and healthcare to finance and technology. In technology companies, it can accelerate software development cycles while maintaining high quality standards. In manufacturing, LLaMA can optimize production processes, reduce defects, and enhance supply chain efficiency. In healthcare, it can streamline patient care pathways, improve clinical outcomes, and minimize errors. In finance, LLaMA can drive process standardization, reduce lead times for financial products/services delivery while ensuring regulatory compliance.
The adaptability of LLaMA makes it a valuable asset for any organization looking to improve its performance regardless of industry or sector.
Challenges in Implementing LLaMA
While the benefits of LLaMA are substantial, implementing these methodologies comes with its own set of challenges. Resistance to change within organizational culture can hinder the adoption of Lean principles or Agile practices. Integrating Six Sigma’s statistical tools may require upskilling employees in data analysis techniques. Additionally, aligning different functional areas within an organization towards a unified LLaMA approach requires strong leadership commitment and effective change management strategies.
Addressing these challenges involves careful planning, stakeholder engagement at all levels within the organization, providing adequate training programs for employees as well as fostering a culture that embraces continuous improvement.
Measuring Success with LLaMA
Measuring the impact of LLaMA implementation is crucial for assessing its effectiveness in enhancing business performance. Key performance indicators (KPIs) such as cycle time reduction, defect rates, customer satisfaction scores, process efficiency improvements should be tracked over time. Additionally, financial metrics such as cost savings from waste reduction or increased revenue from faster time-to-market can provide tangible evidence of the benefits derived from LLaMA adoption.
Regular assessments through audits or reviews help in identifying areas for further improvement while also recognizing successful outcomes achieved through LLaMA initiatives.
Conclusion
In conclusion, leveraging LLaMA methodologies presents a compelling opportunity for organizations seeking to enhance their business performance. The integration of Lean’s waste elimination principles with Agile’s flexibility and responsiveness along with toxsl focus on quality creates a robust framework for driving operational excellence across industries. By embracing a culture of continuous improvement underpinned by strong customer focus, businesses can realize tangible benefits in terms of efficiency gains, cost reductions as well as improved product/service quality.
The journey towards implementing LLaMA may pose challenges but the long-term rewards in terms of sustained competitive advantage make it a worthwhile endeavor for any forward-thinking organization committed to achieving excellence in today’s dynamic business environment.
FAQ's
What is LLaMA and how can it help my business?
LLaMA (Large Language Model Meta AI) is an advanced AI model developed by Meta (Facebook). It can understand and generate human-like text, making it useful for many business tasks like customer support, content creation, data analysis, and more. By using LLaMA, your business can save time, reduce manual work, and improve decision-making.
How does LLaMA improve business performance?
LLaMA boosts performance by automating repetitive tasks, enhancing communication, and delivering fast insights from large amounts of data. For example, it can write reports, create marketing content, or even chat with customers. This helps businesses work smarter, faster, and more efficiently.
Is LLaMA safe and reliable to use in my company?
Yes, LLaMA is designed to be safe and secure. However, like any AI tool, it should be used responsibly. With proper setup and human supervision, LLaMA can become a trusted assistant in your daily operations without compromising data privacy or quality.
Do I need technical skills to use LLaMA in my business?
Not necessarily. While some technical setup may be needed at first, many tools using LLaMA come with user-friendly interfaces. If you partner with an experienced tech company like ToXSL Technologies, we can help you integrate and manage LLaMA smoothly—no deep technical knowledge required.